Equipment grouping for cleaning validation
- Ahmed Ramy, PhD
- Mar 18, 2023
- 3 min read
Equipment grouping is an essential aspect of cleaning validation in pharmaceutical and biopharmaceutical manufacturing. The objective of equipment grouping is to categorize equipment based on their similarities in terms of design, function, and cleaning requirements. This process allows for the development of cleaning validation protocols that can be applied to a group of equipment with similar cleaning requirements, rather than testing each individual piece of equipment.
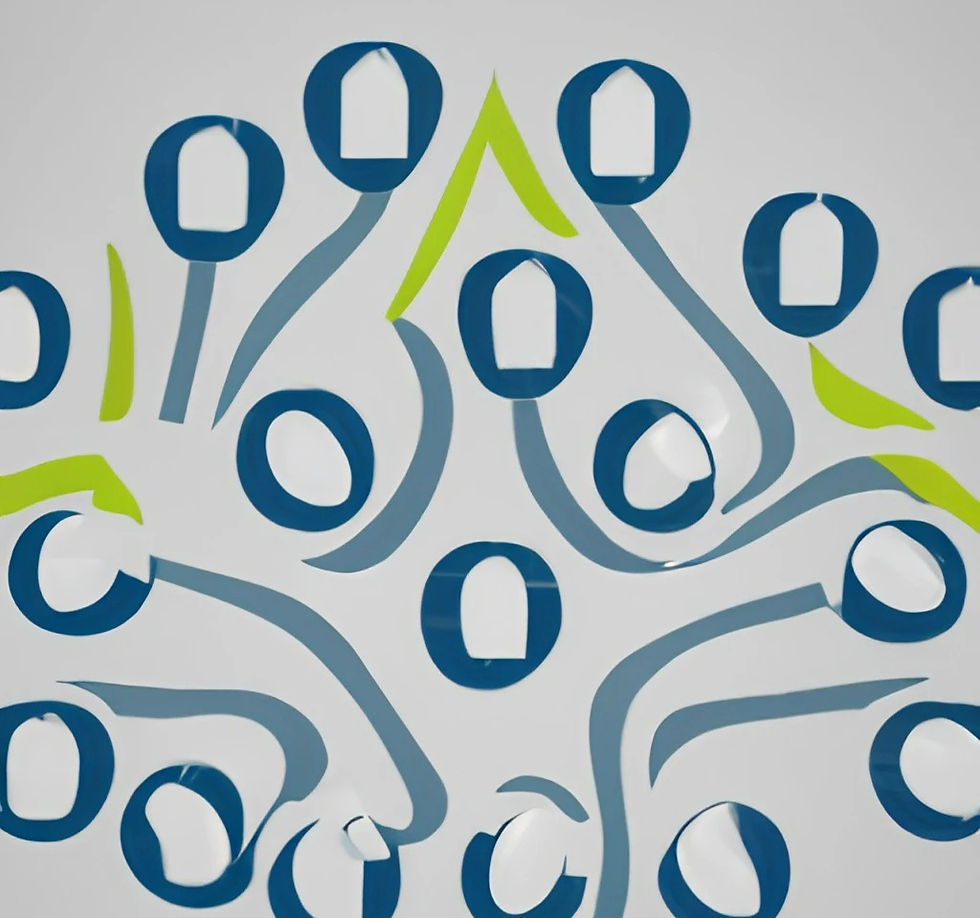
Equipment grouping for cleaning validation involves the following steps: Step 1: Identification of Equipment The first step is to identify all the equipment that needs to be cleaned and validated. This includes all the manufacturing equipment, such as tanks, reactors, filters, and filling machines, as well as the support equipment, such as hoses, gaskets, and valves. Step 2: Classification of Equipment The next step is to classify the equipment based on their design and function. This involves grouping equipment with similar design and function together. For example, all the mixing tanks could be grouped together, while all the filling machines could be grouped together. Step 3: Determination of Cleaning Requirements The third step is to determine the cleaning requirements for each equipment group. This involves identifying the cleaning agents and procedures required to effectively clean the equipment. The cleaning requirements may vary based on the equipment design, material of construction, product contact surfaces, and cleaning agents used. Step 4: Development of Cleaning Validation Protocol The final step is to develop a cleaning validation protocol for each equipment group. This involves specifying the sampling locations, acceptance criteria, analytical methods, and documentation requirements for each equipment group. There are several benefits to equipment grouping for cleaning validation. Firstly, it saves time and resources by reducing the number of validation studies required. Instead of validating each individual piece of equipment, validation can be performed on a representative sample from each equipment group. This allows for a more efficient validation process and reduces the overall validation workload. Secondly, equipment grouping allows for a more robust validation process. By grouping equipment with similar cleaning requirements, the validation protocol can be optimized to ensure that all equipment within the group is effectively cleaned and validated. This helps to ensure that product quality is not compromised by equipment contamination. Thirdly, equipment grouping helps to minimize the risk of cross-contamination. By grouping equipment with similar cleaning requirements, the risk of cross-contamination between different products is reduced. This is particularly important in multi-product facilities, where equipment may be used for different products. In order to ensure effective equipment grouping for cleaning validation, it is important to consider the following factors: Equipment Design: Equipment with similar design and construction should be grouped together. This includes equipment that is made of similar materials, has similar product contact surfaces, and has similar cleaning requirements. Function: Equipment that performs similar functions should also be grouped together. This includes equipment that is used for mixing, filling, and packaging. Cleaning Requirements: Equipment with similar cleaning requirements should be grouped together. This includes equipment that requires similar cleaning agents and procedures. Product Contact: Equipment that comes into contact with similar products should also be grouped together. This includes equipment that is used for the same product or products with similar characteristics. In conclusion, equipment grouping is an essential aspect of cleaning validation in pharmaceutical and biopharmaceutical manufacturing. By grouping equipment with similar cleaning requirements, the validation process can be optimized to ensure that all equipment is effectively cleaned and validated. This helps to ensure product quality, reduce the risk of cross-contamination, and save time and resources. When considering equipment grouping for cleaning validation, it is important to consider equipment design, function, cleaning requirements, and product contact.
Commentaires